Optimizing Inbound Operations with WMS: A Key to Streamlined Workflow
- Linkage Retail Solutions Limited
- Feb 5
- 3 min read
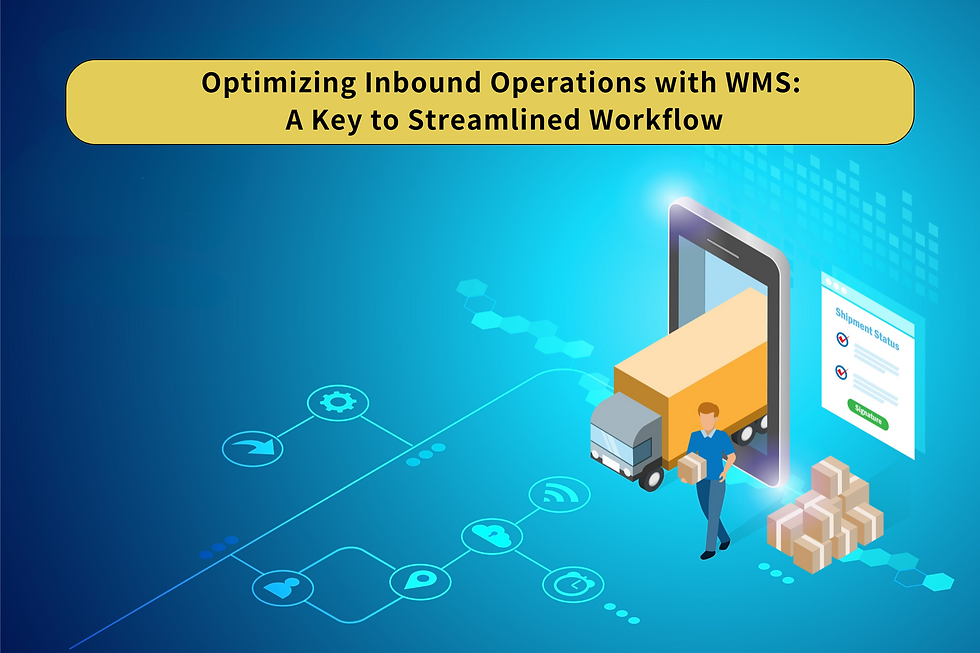
Warehouse management is vital for overseeing all warehouse activities, from inbound receiving and quality inspections to inventory management. Improving this process can boost accuracy, ensure timeliness, and enhance efficiency, and implementing a robust Warehouse Management System (WMS) is a key strategy for achieving this optimization.
By automating warehouse tasks, standardizing operations, and reducing manual processes, errors can be minimized effectively.
How Does a WMS Optimize Inbound Operations?
Inbound Receiving
A Warehouse Management System (WMS) plays a crucial role in overseeing the receiving process. Before goods physically arrive at the warehouse, an Advanced Shipping Notice (ASN) or Purchase Order (PO) is typically sent by the shipper. This document contains essential cargo details such as the estimated arrival date and time, item descriptions, barcodes, packaging specifics, and quantities. Having this information in advance significantly aids in the smooth operation of the receiving process.
Upon the goods' arrival, the implementation of Barcode and Radio Frequency Identification (RFID) systems ensures a seamless and accurate receiving process. The WMS leverages these technologies to instantly cross-reference the goods' information with the data provided in the ASN or PO, ensuring alignment and precision in warehouse operations.
Goods Inspection and Quality Control
Warehouse personnel can establish specific receiving criteria within the Warehouse Management System (WMS), ranging from basic checks like ensuring the integrity of outer packaging to more complicated inspections of individual item quality.
In cases where damaged or faulty products are identified during these assessments, the WMS is equipped to automatically redirect non-compliant items to a designated quarantine zone. This proactive measure helps prevent the intermingling of acceptable and defective goods, maintaining operational integrity and product quality standards.
Put-Away
This process involves transferring goods from the receiving area to the storage area within the warehouse. The WMS plays a crucial role in this task by accurately and efficiently allocating storage locations. It considers various factors such as the type of goods, outbound frequency, dimensions, weight, and other relevant information to determine the most suitable storage locations for optimal organization and ease of retrieval.
Real-Time Visibility of Inventory
The WMS offers real-time and precise insights into warehouse operations, encompassing inbound processes, put-away, storage, outbound procedures, and shipping. During storage, both warehouse staff and customers can access comprehensive details like quantity, expiration dates, descriptions, storage times, and more.
Moreover, the WMS can trigger an automatic replenishment process when inventory levels drop below a predefined threshold, ensuring seamless operations.
Integration with Supplier and 3rd Party Logistics Company
Integrating a WMS with suppliers and third-party logistics (3PL) providers can significantly boost supply chain efficiency and raise customer service standards. Here are some key advantages:
Real-time Data Exchange: Facilitate real-time information sharing, eliminating the need for manual message exchange and ensuring the latest insights are available across the network.
Automatic Replenishment Process: Enables automated replenishment procedures when stock levels near depletion, enhancing inventory management efficiency and preventing stockouts.
Shipment Tracking: Provides seamless shipment tracking capabilities within the integrated system, eliminating the necessity to visit third-party logistics companies for tracking updates and streamlining logistics operations for enhanced transparency and customer satisfaction.
Time to Consider
Are you ready to be more competitive in the market? Get ready to enhance the efficiency, boost the productivity levels and increase customer satisfaction?
Contact us today and we will provide you with professional consulting and technical assistance.
Our Services & Product: https://www.linkage-retail.com/products
You can reach us by:
Webpage: https://www.linkage-retail.com/
WhatsApp: +852 3157 1384
Email: info@linkage-retail.com
Comentarios